Die casting in Malaysia has become an essential component of the manufacturing industry which plays an essential part in the production of high-quality metal components that can be used in a range of. In Malaysia’s efforts to develop its industrial capabilities and capabilities, the process of die casting has been recognized as an essential process for sectors such as automotive, aerospace, electronics, and consumer goods. The ability to create robust and precise components by die casting has enticed multinational and local companies to invest in Malaysia’s manufacturing. With a strong infrastructure, a skilled workforce and government support to boost industrial development, Malaysia has positioned itself as a competitive hub for die casting manufacturing. The companies involved in this business leverage advanced technology and automation to increase efficiency and ensure compliance with global quality standards. With the demand for light, high-performance metal components is increasing, Malaysia’s die casting sector is likely to continue experiencing growth.
One of the major benefits of die casting is the capability to make intricate shapes that are precise and high consistency. The process involves injecting molten metal into a mold cavity with high pressure, allowing manufacturers to make intricate designs using minimal processing. It is an efficient method for production in mass quantities, because it helps reduce waste materials and improves production. The companies in Malaysia’s die casting industry have adopted state-of-the-art machinery as well as innovative methods to increase production efficiency and quality. It has witnessed significant advancements in technology that allows companies to improve their operations and maintain consistency across large-scale production. With the integration of Computer-aided Design (CAD) or simulation tools, companies can optimize mold designs as well as improve results. The technological advances have placed Malaysia as an international leading die casting company, and able of meeting the ever-changing requirements of the global industry.
The automotive industry is one major beneficiaries of die casting in Malaysia, relying on this process to manufacture vital automobile components. Lightweight aluminum and zinc die-cast parts are widely used in contemporary automobiles to increase the efficiency of fuel and decrease the overall weight. Components such as engine blocks, transmission cases as well as structural brackets, are usually made using die casting due to their strength and durability. Malaysia’s strategically located location as well as its established supply chains have attracted major automobile manufacturers to establish production facilities in the country. Demand for precision automotive parts continues to grow, prompting local die casting businesses to invest in research and development. By focusing on material innovation and process improvements, Malaysian manufacturers are able to manufacture high-quality parts which meet the international standards for automotive components. The result has strengthened Malaysia’s standing as a reliable supplier in the international automotive market.
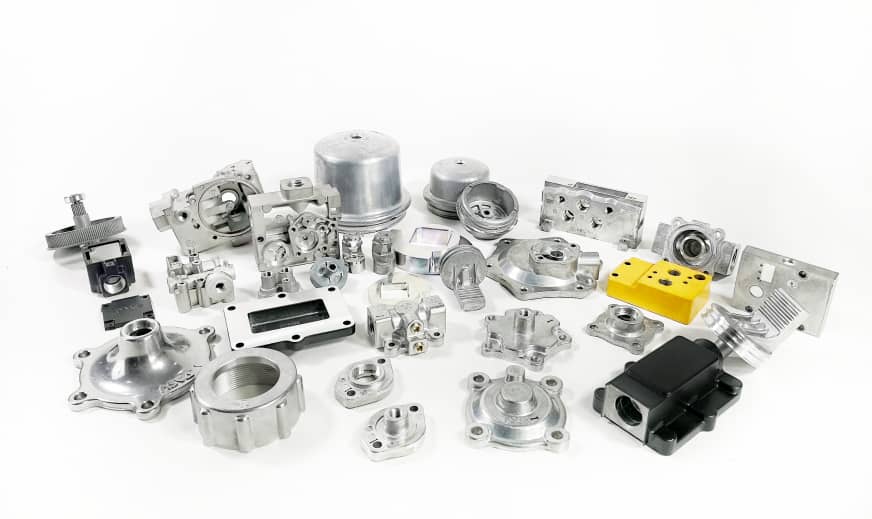
In addition to the automotive sector, the electronics business is also a major part of the economy in Malaysia heavily relies on high pressure diecasting malaysia in manufacturing various parts. Because of Malaysia being the world’s leading exporter of electronic products and components, die-casting is essential for the production of housings, heat sinks and connectors. The quality and efficiency of die-cast aluminum makes it an ideal material for electronic applications that ensure the performance of electronic devices. Growing need for consumer electronics telecom equipment and industrial machinery have further increased the need for high-quality die casting solutions. Malaysian manufacturers have reacted by implementing strict quality control measures and making investments in automated production to satisfy the growing demands of production. Manufacturing electronics that are lightweight and long-lasting has positioned Malaysia as a major participant in the electronic supply chain.
The environmental and sustainability issues have also influenced the industry of die casting in Malaysia which has led businesses to implement eco-friendly processes. With the global push for sustainable manufacturing, die casting firms are looking for strategies to decrease their carbon footprint. Recycling of metals like aluminum and zinc alloys is gaining recognition, since these materials are able to be reused with no loss of quality. Energy-efficient production methods as well as waste reduction efforts as well as cleaner processes for manufacturing have become standard practice within the manufacturing industry. Malaysian producers are investing in green techniques, including electric melting furnaces, as well as closed loop cooling systems, to minimize the use of energy. These efforts are not just a way to improve environmental conservation but also improve cost efficiency and competitiveness in the marketplace. As the demand for sustainable products grows, Malaysia’s casting industry is set to be able to satisfy global demands for greener manufacturing solutions.
The future of die casting in Malaysia looks promising, with technological advancements that continue to keep pace with rising demands from a variety of sectors. The government’s focus on development in the industrial sector, together and foreign investment, has created a favorable atmosphere for the growth of the manufacturing sector. Utilizing smart manufacturing techniques, such as robots, data analytics and artificial intelligence is expected to enhance the efficiency of production and increase productivity. When global markets move towards more lightweight, high-performance materials Malaysia’s die casting industry is expected to play a significant role in providing critical components. With high-quality standards maintained by investing on research and development, and adopting a sustainable approach, Malaysian manufacturers can strengthen their position in the global die casting industry. By pursuing continuous advancement and strategic alliances, Malaysia is poised to remain a competitive force in the industry of die casting for a long time to come.